Inside Clutch Tuning:
"HC-X" Roller Secondary System
"Current constant radius helix technology actually combines two
functions into its design The two functions the helix are required to control are
"Force on the belt" and the "Rate of shift". "Force on the
belt" is the side force needed to stop the belt from slipping against the sheaves.
The "Rate of shift" controls how quickly the sheave faces open up letting the
belt move to different shift points.
Many tuners have experience in balancing these two functions. A shallower helix angle
results in more side force on the belt. This helps to prevent the belt from slipping and
has excellent back shifting characteristics, but also slows the rate Of Upshift.
On the other end of the spectrum are the steeper angled helixes. They provide far more
upshift, but belt slippage at full shift Out is always a problem. This is why multi-angled
helixes are common in most OEM clutching calibrations today. Multi-angled helixes offer a
better solution than a straight angle helix, but many compromises and trade-offs still
exist.
Quite simply, belt squeezing force is achieved at the expense of the rate of shift. In
order to increase the belt squeezing force With Current helixes, we had to introduce a
mechanical interference (shallow helix angle) that slowed the rate of shift. Conversely,
to increase the rate of shift (steeper helix angle) we sacrifice the back shifting. Can't
we get more of both, a better balance?
As mentioned, current helix designs have forced us to balance
the two functions. Figure #5 shows the rate of shift of a straight angled helix and
multi-angled helix.
(click for...)
Figure 5
Rate of Shift
In figure #5, notice how sheave displacement changes at a constant rate as
it shifts out for a straight angled helix. Barring high friction, and aerodynamic losses,
the sled will accelerate at a constant rate. This is not the case for the multi-angle
helix. The sheave displacement starts out shifting at a rapid rate, but as the sheaves
open up and the belt moves down into the sheaves, the rate at which the sheaves open
decreases. In other words, the snowmobile acceleration will decrease as it approaches top
speed.
Many of us have seen classic examples of this. Our sled will accelerate to 100 mph in 1/4
mile, but it takes another 3/4 mile to get to 120 mph. Why is that? The helix design
itself may contain many of' the answers.
The new "Heel-X" roller secondary uses a new (patent pending) design called
"Decreasing Touch Point Technology". The Helix used in this system has four
degrees of freedom (X,Y,Z,R). Current helixes change in three degrees of freedom (X,Y,Z).
As the secondary clutch shifts out and the belt moves down the sheave faces, the touch
point between the roller and helix moves down also. Figure #6 shows the mechanical system
of both the current "constant radius technology" and the "decreasing touch
point technology" as the system shifts out.
(click for...)
Figure 6
Helix Force Illustration
As you can see in both the constant and decreasing radius technologies, the belt pulls on
the secondary clutch due to engine torque. The more torque the engine has the higher the
pull force transferred to the secondary clutch. The distance that the belt is away from
the center of the rotational shaft is a very critical dimension. At the start of the shift
(3.8 shift ratio) the belt is at the top of the secondary sheave. This distance acts as a
torque multiplier at the helix touch point location. As you can see from the equation, as
you increase the distance from the belt pull location to the radius of the helix touch
point force at the helix is very high.
In both technologies the belt pull location is not constant. As the CVT transmission
shifts out, the belt moves down the sheave faces. At the full shift out point the belt and
Helix touch point have become very close. This loss in distance between the
Helix touch point and the belt pull point means the torque multiplication has been
significantly diminished. It's a simple case of the loss of leverage. We have all used a
"Cheater Bar" to loosen a rusted bolt, this works on the same principle.
The Heel-X secondary changes the touch point between the roller and the helix as the belt
moves down the sheave faces. This is a significant change in clutching philosophy.
By changing the radius touch point we can now separate the force on the
belt from the rate of shift.
Heel-X touch point starts out at 58mm from the center of' the shaft location at
the 3.8 shift ratio point, and decreases to 371nni at the full open point. Current Polaris
and Ski-Doo Helixes are a constant 40.mm to the touch point, where Arctic Cat and Yamaha
touch Points are at a constant 45mm.
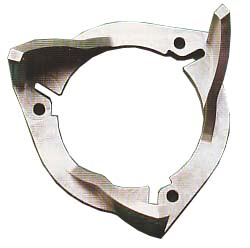
By moving the touch point in to a radius of 37mm, squeezing
force on the bell is significantly increased at the full shift out point. By moving the
touch point out to 58mm at the 3.8 shift ratio point the secondary will shift very
aggressively.
This change in touch points can now be used to simply control the force on the belt only'
We can apply Just enough force to stop the belt from slipping all the way from the 3.8
shift ratio to the full shift out point.
By controlling the force on the belt by changing leverage points, we can now go back to
straight angled helixes and use it Control Only the rate of shift. This is a significant
advantage for Upshifting and backshifting because we have eliminated the mechanical
interference of' the multi-angled helix. Testing has shown that a straight cut 42 degree
Heel-X can [low Out Shift a 62 degree Arctic Cat helix with no belt slippage on the top
end. With no steep helix angle to climb as the roller moves back to the 3.8 shift
ratio, back shifting characteristics are excellent. This is a tuning variable not
previously available to the tuner or CVT manufacturer.
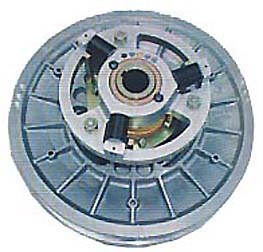
The Heel-X Roller Secondary System is available for Arctic Cat
and Yamaha open-roller secondary clutches, including the Acrtic Cat
"Bearcat". This is a direct bolt-on system with no machining or external
modifications to the secondary Clutch. A hardened steel helix is utilized, with a
replacement roller cover fitted with wide-track rollers to follow the changing helix
radius.
The "HC-X" Driven Clutch Kits were featured in the
December 2001 issue of SnowTech
Magazine.
You may also wish to read:
"Inside Clutch Tuning:
Tune the Primary or the Secondary?"
Authorized Distributor.
(Dealer inquiries welcome.)
To reserve yours or
learn more, visit our website at
www.sledgear.com
|